2rike
Full Member

Posts: 184
|
Post by 2rike on Nov 28, 2015 14:02:35 GMT -5
2rike, I have admiring your panel progress (bucks,molds,panels). Wish you lived around the corner from me. Keep up the good work! To answer your questions, if you use a rear wheel drive differential it needs to be flipped upside down. My C of G is right at the lowest point of the seat, basically where the vehicle "feels" the weight of the occupants. C of G height is nice and low at 17". Width at the front (track) is 81". Thats a great solution to the problem and so simple! Did the propshaft to the front cause you any trouble accommodating a transmission tunnel in the cockpit area? I would like to see some more detailed photos of your RT If you want to share them.
|
|
|
Post by DaveJ98092 on Nov 28, 2015 15:50:05 GMT -5
I seen a RT many years ago that used a Goldwing 1500/6 behind the driver and a Subaru IRS rearend upside down in the front with Subaru IFS front spindles. I would not want to push too much power into an upside down gear set. You are pushing on the "Coast" side. And the Lube is not flowing down the way it was designed. Light weight and lower power, it should work well for most of us. JUST DO NOT USE A LIMITED SLIP (Posi) DIFF. A posi diff will tend to jurk the wheel out of your hands and also make the outside tire try to spin the same speed as the inside tire in a corner and may induce a slide. Just my 2 cents worth.
|
|
2rike
Full Member

Posts: 184
|
Post by 2rike on Nov 28, 2015 16:48:32 GMT -5
I suppose changing the diff oil will have its challenges with the filler and drain plug in the wrong orientation!
|
|
|
Post by Liteway on Nov 28, 2015 18:12:34 GMT -5
I seen a RT many years ago that used a Goldwing 1500/6 behind the driver and a Subaru IRS rearend upside down in the front with Subaru IFS front spindles. I would not want to push too much power into an upside down gear set. You are pushing on the "Coast" side. And the Lube is not flowing down the way it was designed. Light weight and lower power, it should work well for most of us. JUST DO NOT USE A LIMITED SLIP (Posi) DIFF. A posi diff will tend to jurk the wheel out of your hands and also make the outside tire try to spin the same speed as the inside tire in a corner and may induce a slide. Just my 2 cents worth. I'm thinking if you do have not have some form of limited slip, your traction ,especially in corners ,will be limited with high power and fwd. In production front drivers with a typical 60/40 weight distribution, It's already a problem for sporty hot hatches with an open diff such as the Mazda speed 3, also infamous for torque steer. That's why the next generation will be going to AWD for the Speed 3 and Focus RS. Even with limited slip fwd (v dub GTI) and lots of weight over the drive wheels, traction can still be problem as weight transfers rearward under power and the front unloads. If the road surface offers limited traction, such as ice, snow, gravel, sand ,acceleration induced weight transfer in not a big factor and FWD works fine.
|
|
|
Post by mtntech on Nov 29, 2015 0:57:39 GMT -5
I seen a RT many years ago that used a Goldwing 1500/6 behind the driver and a Subaru IRS rearend upside down in the front with Subaru IFS front spindles. I would not want to push too much power into an upside down gear set. You are pushing on the "Coast" side. And the Lube is not flowing down the way it was designed. Light weight and lower power, it should work well for most of us. JUST DO NOT USE A LIMITED SLIP (Posi) DIFF. A posi diff will tend to jurk the wheel out of your hands and also make the outside tire try to spin the same speed as the inside tire in a corner and may induce a slide. Just my 2 cents worth. In this scenario you are not "pushing on the coast side". Diff is still turning the same way it was intended, it just flipped upside down. On a Subaru diff even the back cover is flippable. The only concern is adequate lubrication to the forward pinion bearing.
|
|
|
Post by DaveJ98092 on Nov 29, 2015 1:07:16 GMT -5
In this scenario you are not "pushing on the coast side". Diff is still turning the same way it was intended, it just flipped upside down. On a Subaru diff even the back cover is flippable. The only concern is adequate lubrication to the forward pinion bearing. You are right. I was thinking on how running a rear diff in the front backwards, not upside down. On the Stupidroo Diff, that same diff is used in many other Japanese cars too. Very stout small diff.
|
|
|
Post by DaveJ98092 on Nov 29, 2015 1:33:08 GMT -5
I'm thinking if you do have not have some form of limited slip, your traction ,especially in corners ,will be limited with high power and fwd. In production front drivers with a typical 60/40 weight distribution, It's already a problem for sporty hot hatches with an open diff such as the Mazda speed 3, also infamous for torque steer. That's why the next generation will be going to AWD for the Speed 3 and Focus RS. Even with limited slip fwd (v dub GTI) and lots of weight over the drive wheels, traction can still be problem as weight transfers rearward under power and the front unloads. If the road surface offers limited traction, such as ice, snow, gravel, sand ,acceleration induced weight transfer in not a big factor and FWD works fine. In the front wheel drive racecars I have built over the years, having posi-traction up front is nice in a straight line. But get it in a corner and punch it hard and it will try to rip the steering wheel out of your hands. Just use caution if you do use one. Torque steer is a huge problem in unequal length drive shafts, a bit less in equal length units but its still there. Again, Posi does help in straight line launch.
|
|
|
Post by Liteway on Nov 29, 2015 10:20:15 GMT -5
I yeild to your practical experience. I am curious about the type/class of racing you competed in and would like to hear more about it. In the days before AWD was improved to the state it is now, and the cars were relatively low powered, FWD road rally cars were the hot ticket. And there was also the old fwd Miller Indy cars of the 1920s and 30s.
As for steering with a limited slip, I was going on press reviews of the latest GTI with an electronically controlled torque sensing diff. I think this addresses the self steering issues you point out with fwd locking differentials but is probably not relevant to our discussion of fwd in home built applications.
Even Ford's more primitive approach of controlling wheel spin through electronically controlled brake application on the spinning side (Focus ST) may be too difficult to make work for us garage rats.
|
|
|
Post by DaveJ98092 on Nov 29, 2015 12:29:05 GMT -5
I had two FWD 1984 Dodge Shelby Chargers that were not Turbocharged and close ratio 5 speeds. I ran one in Rally-Cross in the Rally Prepared class where I could do just about anything as long as the car stayed street legal. I used Ford F250 springs up front and Ford Fairmont stationwagon rear coil-overs as this combo looked stock and raised the car 1.5 inches. I used a device called Phantom Grip that gave me some positraction effect. Car weighed just at 2000 pounds with me in it and had about 210 horsepower out of a 11.2:1 compression 2.2 liter with Headder hot camshaft and Holly 390 carb.
The other Shelby I drove on the street and drag raced almost every other week. Almost same engine build but a much milder canshaft, about 175 Horsepower. It weighed about 2400 pounds with me in it, carpet and sound deadener. It would pull mid to high 14 second quarter mile. In its day it was one of the fastest FWD cars in the nation but I could not afford to run in the NHRA Division races so I stayed local. This car went with me to Germany and back when I was stationed over there. The Autobahn was fun.
|
|
|
Post by mtntech on Nov 29, 2015 14:00:24 GMT -5
In this scenario you are not "pushing on the coast side". Diff is still turning the same way it was intended, it just flipped upside down. On a Subaru diff even the back cover is flippable. The only concern is adequate lubrication to the forward pinion bearing. You are right. I was thinking on how running a rear diff in the front backwards, not upside down. On the Stupidroo Diff, that same diff is used in many other Japanese cars too. Very stout small diff. First time I saw that diff was in a Datsun 510. What years were you in Germany? I was there from 86-90 and 91-92. I too had a blast driving there. I'll try and dig up some pics.
|
|
|
Post by DaveJ98092 on Nov 29, 2015 15:46:10 GMT -5
Heidelberg 1975-1976 Stuttgart 1979-1983 Kaiserslautern 1987-1990
|
|
|
Post by mtntech on Nov 29, 2015 20:07:51 GMT -5
This was my funnest ride over there. A lightweight Euro spec 930 with a whole bunch of upgrades. A true 173 mph car. 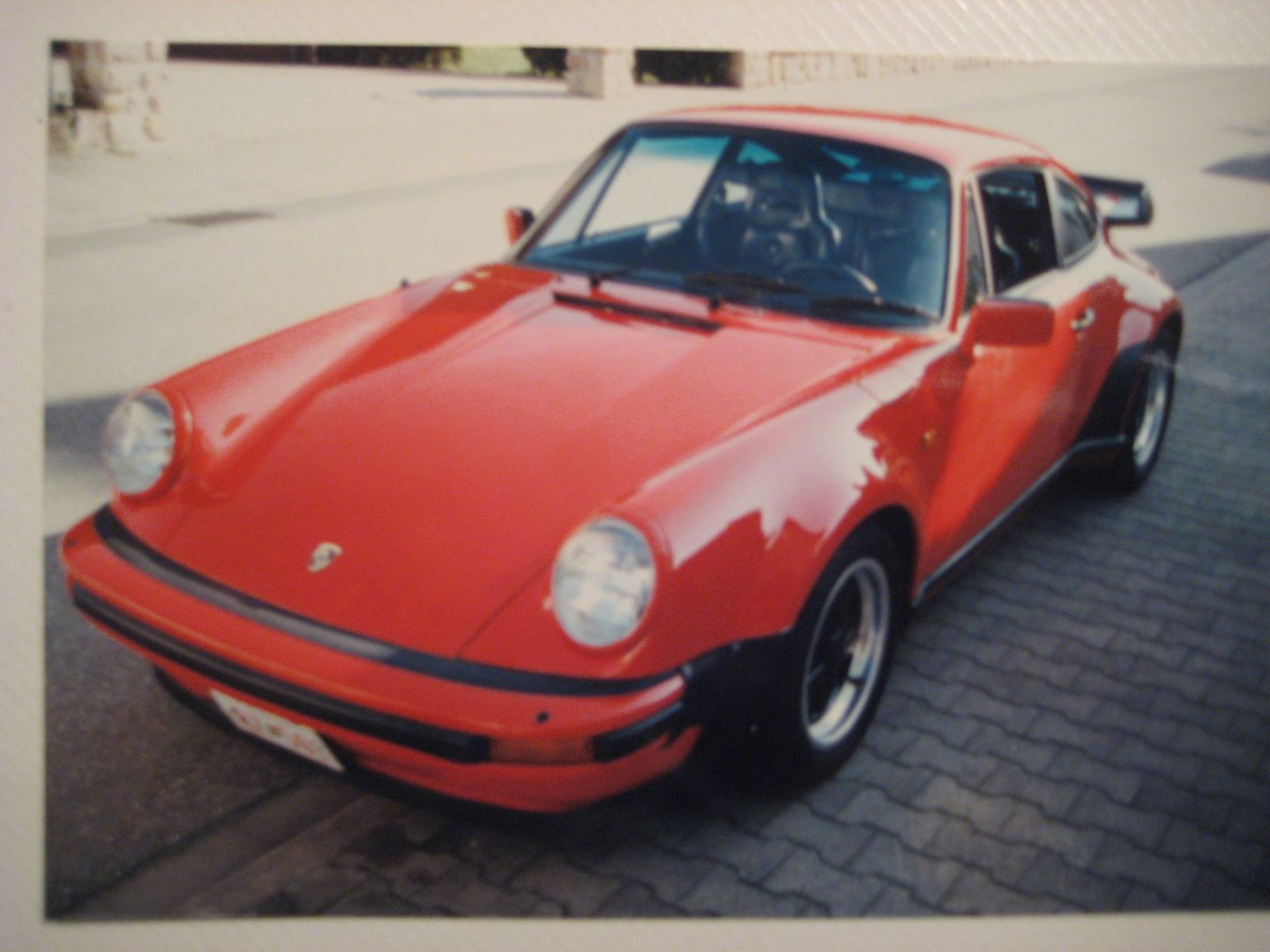
|
|
|
Post by mtntech on Nov 29, 2015 20:48:13 GMT -5
2rike, I have admiring your panel progress (bucks,molds,panels). Wish you lived around the corner from me. Keep up the good work! To answer your questions, if you use a rear wheel drive differential it needs to be flipped upside down. My C of G is right at the lowest point of the seat, basically where the vehicle "feels" the weight of the occupants. C of G height is nice and low at 17". Width at the front (track) is 81". Thats a great solution to the problem and so simple! Did the propshaft to the front cause you any trouble accommodating a transmission tunnel in the thingypit area? I would like to see some more detailed photos of your RT If you want to share them. I am running a Tremec TKO600 transmission at the moment. I went this way because there is a paddle shifter kit available for this transmission. Remember, at present my shift pattern is reversed because the transmission is installed backwards in the chassis. After driving it for the summer I am fully used to it. I think I will go back to a Honda S2000 transmission. It will be smoother and quieter. It was not a big problem to route the gearbox between the seats. I did try to keep the occupant area as narrower as possible.
|
|
|
Post by mtntech on Nov 29, 2015 20:54:23 GMT -5
I had two FWD 1984 Dodge Shelby Chargers that were not Turbocharged and close ratio 5 speeds. I ran one in Rally-Cross in the Rally Prepared class where I could do just about anything as long as the car stayed street legal. I used Ford F250 springs up front and Ford Fairmont stationwagon rear coil-overs as this combo looked stock and raised the car 1.5 inches. I used a device called Phantom Grip that gave me some positraction effect. Car weighed just at 2000 pounds with me in it and had about 210 horsepower out of a 11.2:1 compression 2.2 liter with Headder hot camshaft and Holly 390 carb. The other Shelby I drove on the street and drag raced almost every other week. Almost same engine build but a much milder canshaft, about 175 Horsepower. It weighed about 2400 pounds with me in it, carpet and sound deadener. It would pull mid to high 14 second quarter mile. In its day it was one of the fastest FWD cars in the nation but I could not afford to run in the NHRA Division races so I stayed local. This car went with me to Germany and back when I was stationed over there. The Autobahn was fun. I remember the Shelby Chargers. Those had some pretty bad torque steer, as did most of the front wheel drive vehicles of that era, foreign and domestic. Things have changed alot in 30 years.
|
|
|
Post by DaveJ98092 on Jan 30, 2016 18:53:09 GMT -5
Another question to ask. What wall thickness do all the builders on here use and why? Some of the Euorpian kits I have see use a wall thickness of 2 mm or about 0.0787 inch thick. I guess if the trike is extremely light weight and powered down low enough that the impact speeds are not high then OK, what do you think?
|
|
|
Post by Liteway on Jan 30, 2016 21:29:16 GMT -5
I used everything from .035 to .095 on mine , the latter reserved for the swing arm and engine mount locations. I used .065 most places. Most tubes are not subject to bending loads, so I did not see a reason to beef up. As I have but one die for the bender, most tubes are 1.125" dia. The main tubes of the swing arm are 2" ers. i1291.photobucket.com/albums/b560/dufffus/First%20%20config/construction/IMG_0679_zps7a70a956.jpg[/IMG][/URL] 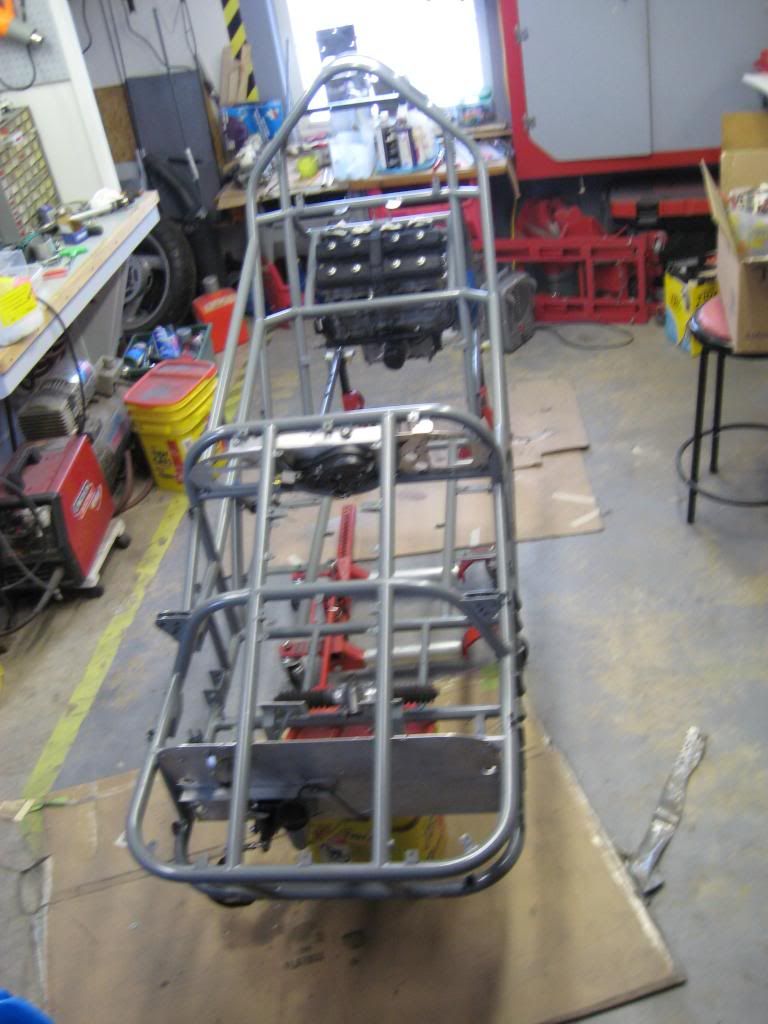 The only two other significant structural elements are a piece of .080 alu. sheet bolted in between the front wheels to form the front of the footwell and help deal with suspension loads there ( It, in turn is bolstered with some .125 alm. plate to mount the master cylinders) and a sheet of .050 across the bottom , nose to engine, that was applied using about 40 small sheet metal screws to make it removeable for modifications. 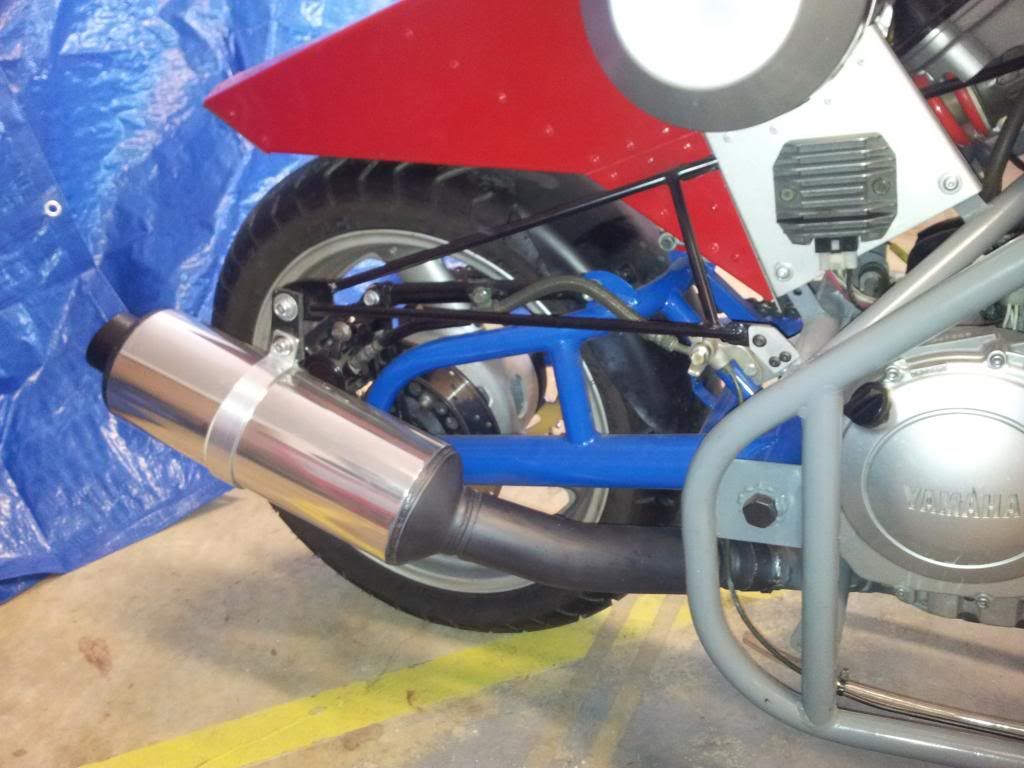 Even the muffler hanger is 3/8" tube, not rod.
|
|